Oven thermal profiling using highly-accurate heat flux sensors
Industrial and residential ovens require a consistent thermal environment to maintain food quality and improve cooking performance. Thistle Thermal Profiling & Hukseflux have collaborated to deliver the Voyager product, an advanced oven thermal profiling system.
Read the full article here: Oven thermal profiling using highly-accurate heat flux sensors (PDF)
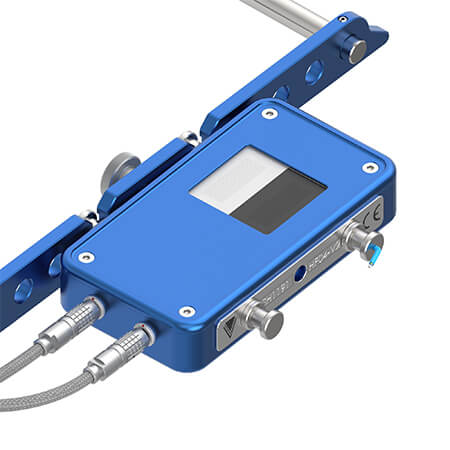
Hukseflux’s FHF05 series heat flux sensors to provide valuable data on
heat transfer inside the oven.
Thermal conditions inside an oven
The thermal environment in industrial ovens is highly variable. A thermal profiling tool like Thistle’s Voyager oven profiling system can help to gather valuable information about the thermal conditions inside the oven. With the use of FHF05 series heat flux sensors, Hukseflux and Thistle have worked together to enhance this thermal profiling tool.
Oven thermal profiling
Oven thermal profiling involves the measurement of key variables that affect the baking process. These variables include:
- radiative and convective heat flux
- product core temperature
- conveyor belt temperature
- air velocity, temperature, and humidity
Measurements of these variables are commonly done during production, such that measurement instruments undergo the same conditions as the product. This allows operators to create a thermal profile of the oven. Furthermore, the Voyager sensor heads can face up or down enabling the independent measurement of both top and bottom heat flux profiles.
While measuring temperature is an essential process parameter, it alone cannot characterise a process. In contrast, heat flux provides insights into the mode, intensity, and direction of heat transfer.
Ideally, this heat flux is separated into their respective components of radiation, convection, and conduction.
There are many benefits to monitoring these variables. Some of them include:
- product consistency and quality
- detection of faulty heating elements
- guaranteeing food safety and compliance
- optimisation of energy consumption
- faster relocation of production facilities
Methods of heat transfer
The main methods of heat transfer in industrial ovens are radiative and convective heat fluxes, see Figure 2. In most applications, conductive heat flux is of lesser interest compared to the other – more fluctuating – methods of heat transfer.
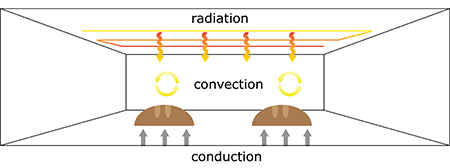
an oven. Radiative and convective heat flux are most important due to
their variability.
Both radiative and convective components can be measured using FHF05 series heat flux sensors that are incorporated into the Voyager thermal profiling system. By covering the sensors with a black or silver coating, they will either fully absorb or reflect thermal radiation respectively.
Consequently, a black-coated heat flux sensor measures the combined heat flux due to convection and radiation, while a silver-coated heat flux sensor measures only the convective heat flux component. Subtracting these values allows for calculation of the radiative component.
Since each type of heat transfer has a different effect on the baking product, it is crucial to separate them for an optimal thermal profile.
Voyager thermal profiling system
Thistle’s Voyager oven profiling system combines the measurement data with intuitive software that allows for fast and easy readout. The data is displayed both graphically and analytically, but can also be easily exported for further analysis.
Moreover, components are available in various sizes to address height constraints inside an oven. Thicker sensor heads combined with a larger thermal barrier allow for longer processes.
For example, the 25 mm sensor head is particularly useful for the biscuit industry, while the 60 mm sensor head is more suitable for longer processes such as bread baking.
Next to the heat flux sensor heads, Thistle also supplies the framework to install a data logger protected by a thermal barrier. See Figure 3. Other components include:
- conditioning unit to pre-heat the sensors
- cables and temperature adapter
- pan brackets for sensor installation
- transport case
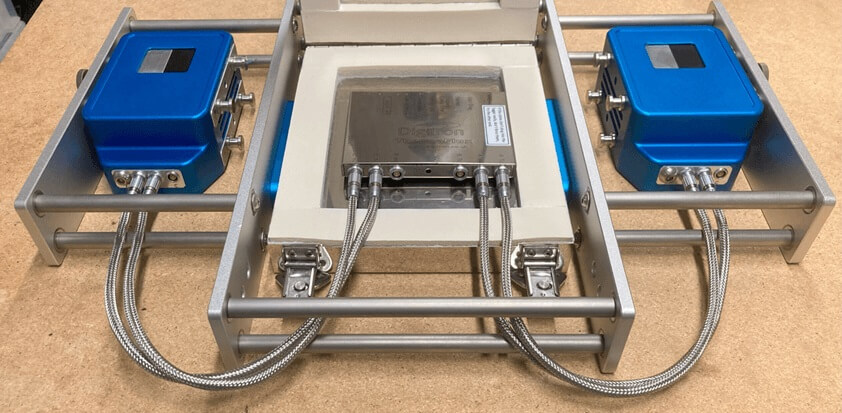
Besides heat flux measurements, Thistle also offers further insights using a temperature bar that can be used to measure the air temperature across the conveyor belt.
Vantage camera system
Another valuable tool is Thistle’s unique Vantage camera sytem that has been developed for monitoring the baking product inside the oven during production. See Figure 4.
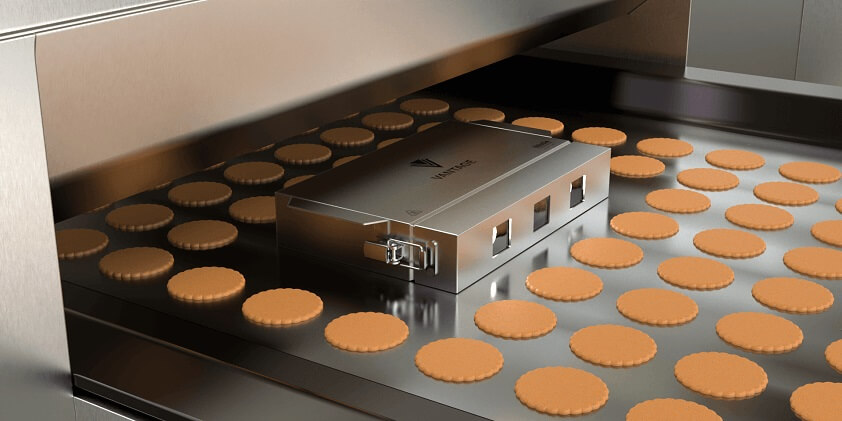
The camera’s integrated lights can be used to obtain information regarding the oven’s status and integrity. With lights off, the camera can monitor the performance of ribbon burners.
Heat flux data for oven thermal profiling
The Voyager system designed by Thistle uses FHF05 series heat flux sensors to provide crucial data for oven thermal profiling. Among the numerous benefits listed, reduced downtime and improved efficiency are the most notable.
The system may be used in combination with the Vantage camera system to compare the heat flux data with visual effects. Ultimately, Thistle’s Voyager system, equipped with heat flux sensors and the Vantage camera system, are essential instruments for oven thermal profiling.
Read the full article here: Oven thermal profiling using highly-accurate heat flux sensors (PDF)