The power of heat flux: improving automotive systems
Heat flux plays a crucial role in automotive systems, impacting the thermal management of components such as engines, batteries, and exhausts. Proper control of heat transfer is essential to maximise efficiency, safety, and performance. As automotive systems become more advanced with improved engines, electric vehicle (EV) batteries, and sophisticated electronics, understanding heat transfer has become increasingly crucial. This article explores the significance of heat flux measurements in automotive systems, their applications, various measurement techniques, and future innovations.
What is heat flux?
Heat flux is the rate of heat energy transfer per unit area, typically measured in watts per square meter (W/m2). In automotive systems, heat flux measurements help understand how heat moves through various components, such as engines, batteries, radiators, or brakes. Factors impacting the heat flux include temperature difference, humidity, and material properties. Measuring heat flux is crucial for evaluating a system's heat management efficiency and its impact on vehicle performance and safety. Read the article What is heat flux? for more detailed information.
Why heat flux measurements matter in automotive systems
Automotive systems are highly complex; they operate with several components that generate heat. Overheating can lead to mechanical failures, degrade materials, and reduce the performance of combustion engines or EV batteries. On the other hand, insufficient heat can also negatively impact the performance, especially in cold weather conditions. Therefore, analysing and managing heat flux is vital for:
- Design: Automotive systems require precise heat management during the design phase to ensure that heat flows are controlled and directed efficiently. Understanding heat transfer helps optimise the layout of components, cooling systems, and select the right materials.
- Efficiency: Efficient thermal management optimises energy use and reduces unnecessary heat losses, leading to improved vehicle performance, whether in electric or traditional combustion engines. This efficiency translates into better fuel efficiency or extended battery range, making vehicles more energy-efficient and cost-effective to operate.
- Safety: Overheating of components such as brakes or batteries can lead to brake failure or battery fires.
- Durability: Excessive heat can shorten the lifespan of materials, leading to premature failure of automotive parts.
- Comfort : Heat flux measurements contribute to the thermal management inside the cabin, ensuring passenger comfort through optimised HVAC (heating, ventilation, and air conditioning) systems.
Key areas where heat flux measurements are crucial
Heat flux measurements are necessary in various automotive parts to monitor and control heat transfer, ensuring optimal performance and safety. Below are some of the most important areas where these measurements are applied:
1. Combustion engines
In traditional gasoline or diesel engines, a large amount of energy is lost as heat during combustion. Heat flux measurements help analyse how much heat is wasted and how it affects the engine’s overall performance. By identifying areas where heat loss occurs, automotive engineers can design more efficient engines with better heat management systems, such as improved cooling or insulating techniques for specific parts.
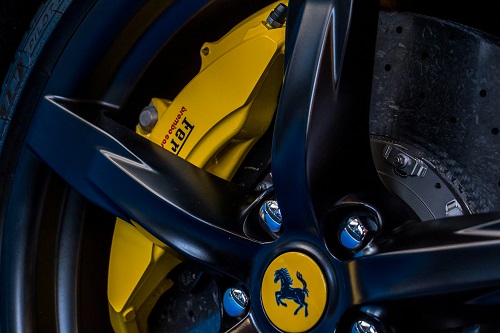
2. Braking systems
All objects with a mass and velocity have kinetic energy. Brake systems convert kinetic energy into heat through friction, bringing the vehicle to a stop. During intense braking, particularly in F1 or heavy-duty vehicles, heat builds up quickly. Excessive heat causes brake fade, which reduces brake efficiency and poses safety hazards. Measuring heat flux in brake pads and rotors allows engineers to design braking systems that can handle more heat while maintaining performance.
3. Electric vehicle (EV) batteries
The rapid rise of EVs has introduced new thermal challenges, particularly regarding the thermal management of lithium-ion batteries. EV batteries generate a vast amount of heat during charging and discharging. If the battery temperature is too high, it can lead to thermal runaway, a dangerous process that can cause fires or explosions. Heat flux measurements are critical in the design of EV batteries to ensure effective battery thermal control, improving safety, extending battery life, and optimising overall vehicle performance.
Tools for measuring heat flux in automotive systems
Various measurement techniques are used to measure heat flux in automotive systems. The choice of a measurement device depends on the component being analysed, the temperature range, and desired accuracy. Below are some commonly used heat flux measurement techniques in the automotive industry:
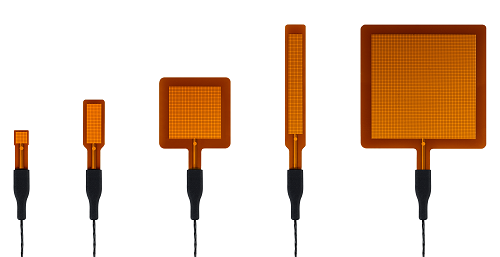
each with different dimensions and sensitivities.
1. Heat flux sensors
Heat flux sensors are widely used to measure the rate of heat transfer. Most Hukseflux heat flux sensors feature integrated temperature sensors, providing simultaneous heat flux and temperature data. These sensors operate through a thermopile that generates a small voltage proportional to the heat flux passing through it. When placed on a surface, the sensor detects both the heat flux and surface temperature. Standalone temperature measurements provide a static snapshot of the temperature at a specific point. Heat flux measurements provide insight on the dynamic rate of heat transfer.
In automotive systems, controlling the flow of heat is often more important than knowing the temperature. While temperature sensors indicate if a component is too hot or cold, heat flux sensors help engineers understand how much heat is being transferred and where improvements in cooling or insulation can be made. Hukseflux offers high-end heat flux sensors, such as the FHF05 series foil heat flux sensors (see Figure 2), designed for various applications, including automotive thermal management. These sensors have been successfully used in real-world scenarios, helping engineers design more efficient and reliable systems.
2. Thermocouples
Thermocouples are sensors that measure temperature, and this data can be linked to heat flux. While thermocouples do not directly measure heat flux, they can measure the temperature difference between two points. This temperature difference can be used to derive heat flux if the thermal conductivity and thickness of the material is known. In many applications, thermocouples are used in combination with heat flux sensors to provide an even better understanding of the heat transfer.
3. Thermal cameras
Thermal cameras, also known as infrared cameras, are used to visualise temperature distribution across a surface. While they do not measure heat flux directly, high and low heat flux can be inferred from analysing hot and cold spots. However, deriving the heat flux value from infrared images requires additional information, such as the material’s thermal conductivity and thickness. This process is less direct and accurate compared to heat flux sensors, which provide precise, real-time measurements.
Thermal cameras are a great addition to heat flux sensors as they offer a broad visual overview of temperature distribution. But for accurate measurements of heat transfer, heat flux sensors are indispensable.
4. Computational Fluid Dynamics (CFD) simulation
In addition to physical sensors, engineers often try to model heat flux in automotive systems with CFD simulations. While high-quality simulations can provide the most detailed insights into how heat moves through materials, they are quite difficult to achieve. The complexity of fluid behaviour and heat transfer makes it computationally intensive to solve, requiring a lot of computational power and specialised knowledge, which may not be available to all engineering teams.
Additionally, most simulations require assumptions to be made to reduce computational load. This requires validating the model with heat flux sensors to assess whether the assumptions are justifiable and to understand their influence on the results. Furthermore, by using data from these sensors, engineers can refine and improve their models, leading to more accurate predictions.
Key innovations shaping the future of heat flux management
Several emerging technologies are transforming how heat flux is managed in automotive systems, with some of the most groundbreaking ones being listed below.
1. Artificial Intelligence (AI)
Artificial Intelligence (AI) is revolutionizing heat flux management in automotive systems by enabling predictive and adaptive thermal control. AI algorithms analyze vast amounts of data from sensors to predict heat generation patterns in critical components like batteries and engines, allowing for proactive cooling measures that prevent overheating and optimize performance.
2. Nanotechnology and advanced materials
Nanotechnology and advanced materials are transforming thermal management in automotive systems. Nano-enhanced composites and coatings improve thermal conductivity and heat dissipation, enhancing the performance and durability of components like engines and batteries. Advanced cooling fluids, such as nanofluids, offer superior heat transfer capabilities. Phase change materials (PCMs) help regulate temperatures by absorbing and releasing heat, while self-healing thermal interfaces ensure reliable and consistent heat transfer over extended periods. Together, these innovations optimise cooling, improve fuel efficiency, and extend component lifespan, playing a crucial role in managing heat in increasingly complex automotive systems.
3. Microchannel heat exchangers
As automotive systems - especially EVs - require more compact and efficient heat management designs, microchannel heat exchangers have become essential. They offer high surface areas for better heat transfer and cooling in small spaces. Hybrid systems that combine liquid, air, or PCM cooling methods provide even greater control over heat management, ensuring that critical components stay within safe temperature ranges.
Conclusion
In conclusion, heat flux measurements are critical for the performance, safety, and efficiency of modern automotive systems. Accurate heat flux data allows engineers to manage the thermal environment of combustion engines, EV batteries, or braking systems.
The application of advanced sensors, simulation tools, and emerging technologies like AI, nanotechnology, and thermoelectric generators is shaping the future of thermal management in the automotive industry.
As vehicles become more complex, particularly with the rise of electric systems, the role of heat flux measurement will only grow in importance, ensuring continued innovation and reliability in automotive design.
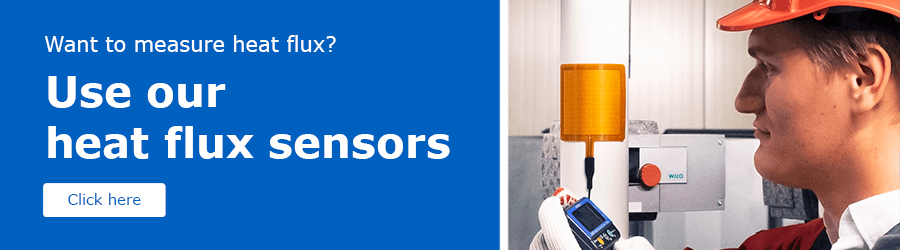