Enhancing composite curing with heat flux sensors
Swinburne University of Technology and Boeing successfully developed an AI-driven framework to optimise composites manufacturing. Reliable heat flux measurements were essential for real-time production monitoring. Therefore, Hukseflux’s FHF06 high-temperature heat flux sensor was selected for its accuracy, fast response time, and proven reliability in demanding industrial environments.
Read the full article here: Enhancing composite curing with high-temperature heat flux sensors (PDF)
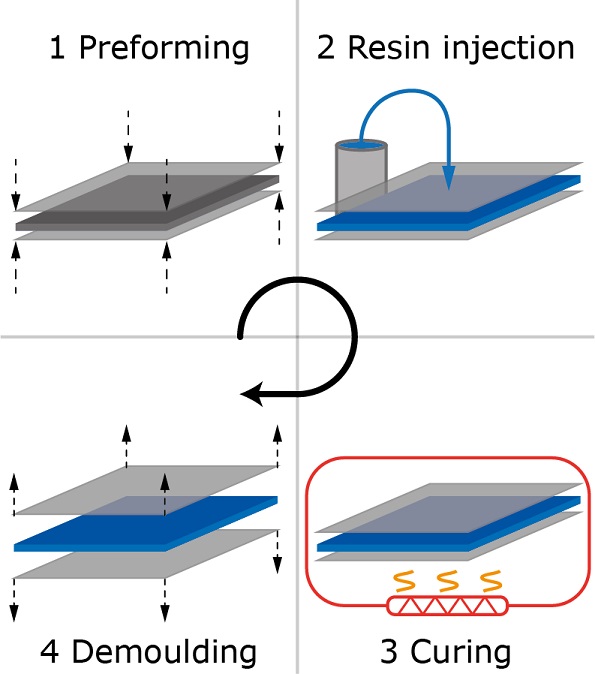
Real-time monitoring of thermal conditions
Composite materials are crucial for high-performance sectors such as aerospace and automotive. However, their production quality relies heavily on thermal conditions, making real-time monitoring essential. To address this, Swinburne University of Technology and Boeing collaborated to create an AI-driven framework for real-time monitoring and forecasting using Hukseflux’s FHF06 heat flux sensors.
Composite manufacturing basics
Composites are formed by combining reinforcing fibres with a matrix material that binds them together. This results in strong, durable materials which are widely applied in many industries.
One commonly used manufacturing method is Liquid Composite Moulding (LCM), which involves four stages (see Figure 1):
- preforming: reinforcement fibres are placed into a mould to form the desired shape
- resin injection: the mould is filled with hot liquid resin. A constant temperature is maintained to ensure effective resin flow through the fibre layers
- curing: the composite is heated until the optimal degree of cure is reached. Curing conditions are critical to final composite quality
- demoulding: after curing, the composite is removed from the mould and is ready for use
The manufacturing conditions during LCM significantly affect the final composite properties.
Swinburne University researchers developed an AI-based framework to accurately monitor and forecast these conditions, enhancing process control by allowing timely adjustments of production parameters. For this, the researchers used FHF06 heat flux sensors, selected for their accuracy and short response time.
Using heat flux sensors in thermal monitoring of composites
Heat flux measurements provide valuable insights into the LCM process. Therefore, heat flux sensors are gaining traction in the composite industry. They are mainly utilised during the resin injection and curing stages.
Heat flux sensors can monitor the resin flow front during the injection stage. This enables early defect detection and allows fine-tuning of injection parameters, such as pressure and flow rate, which can reduce production costs. Since changes in heat flux precede temperature changes, heat flux sensors yield more accurate and faster flow front detection than temperature sensors.
Heat flux also plays a key role in the curing stage. Most curing processes are exothermic, meaning that they release heat. Therefore, curing progress can be monitored by measuring the resin’s heat production, which can be determined through combined heat flux and temperature measurements.
Explaining the AI-driven monitoring framework
Researchers at Swinburne University collaborated with Boeing to streamline LCM manufacturing methods using AI-driven predictions.
The AI-driven framework consists of three core components:
- specialised sensors measure critical parameters such as temperature, heat flux, and resin flow progression
- an Internet of Things (IoT) platform enables real-time data acquisition, processing, and cloud storage
- an AI model predicts future process states, such as the resin curing progress and temperature profiles
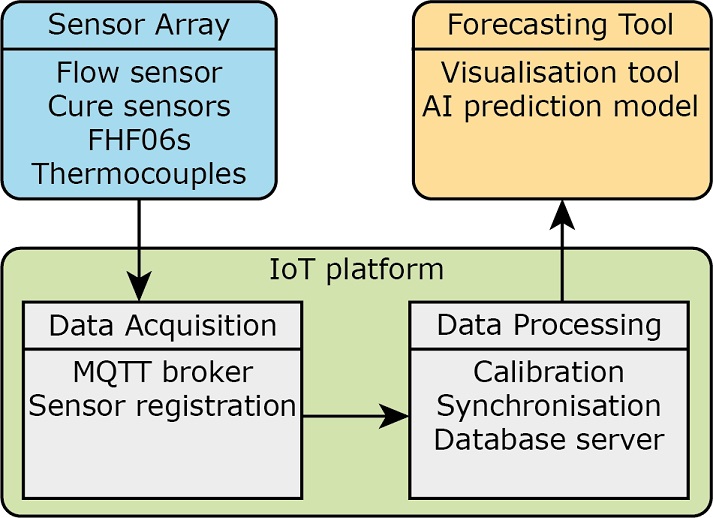
The researchers tested the framework in a real-world manufacturing case study. The results demonstrate that this framework is a promising candidate for digitalised composite manufacturing.
FHF06 high-temperature heat flux sensors
For reliable forecasting, the researchers required accurate and sensitive sensors. Therefore, they selected Hukseflux's FHF06 heat flux sensors. The sensor can withstand temperatures up to 250 °C, while maintaining excellent accuracy and fast response times. These properties make the FHF06 ideal for high-precision composite curing applications.
Additionally, the sensitivity of the FHF06 ensures that even small changes in the heat flux can be measured. Combined with fast response times, this allows for timely detection of resin flow fronts during the injection stage. Therefore, the FHF06 also provides a solution for resin flow front monitoring.
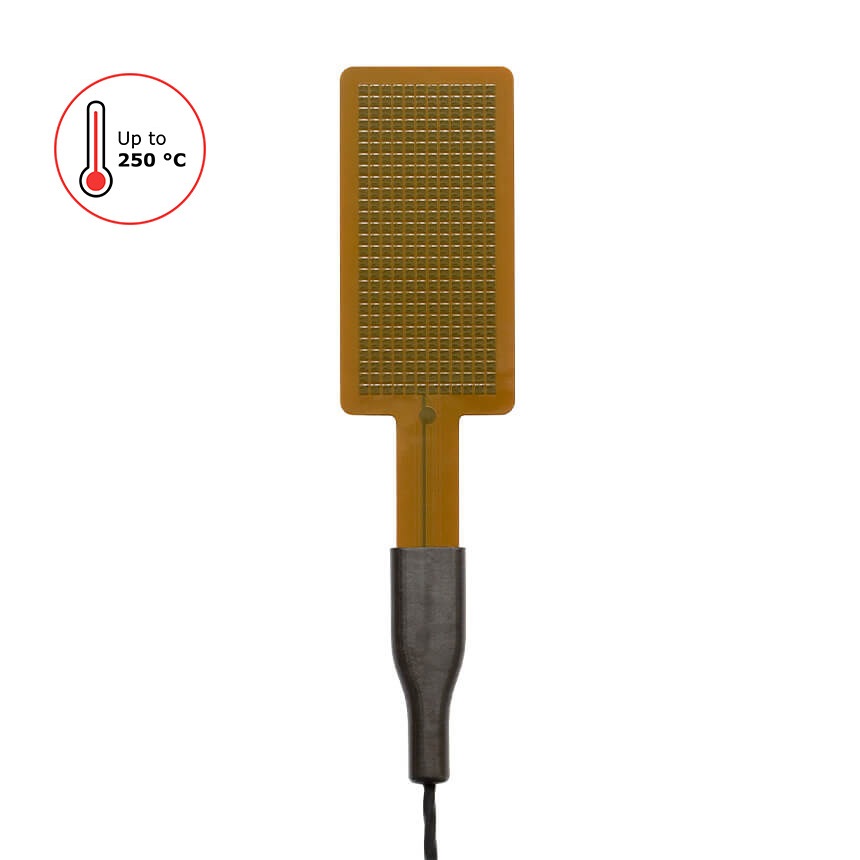
In summary, the FHF06 heat flux sensor has proven to be a valuable tool in the composite manufacturing industry. It is suitable for critical process stages such as the resin injection and curing stages. The innovative study conducted by Swinburne University and Boeing highlights the applicability of the FHF06 in high-accuracy composite manufacturing and research.
Read the full article here: Enhancing composite curing with high-temperature heat flux sensors (PDF)