Measuring heat flux in industrial furnaces
Industrial furnaces, such as those used in the steel or petrochemical industry, play a crucial role in modern industrial processes. These systems require precise heat flux measurements to ensure safety, efficiency, and longevity. Accurately measuring heat flux in these furnaces is vital for optimising design, preventing equipment failure and reducing emissions, which ultimately saves costs.
This article dives into common measurement techniques, the importance of heat flux measurements in industrial furnaces, and the associated challenges. We will also provide an overview of the different heat flux sensors Hukseflux offers.
Why heat flux measurements outperform other techniques in industrial furnaces
Probe measurements
Furnaces that operate with impinging jet flames often reach high temperatures. A common method to measure the flame’s temperature is inserting probes into the flame, but this process presents difficulties due to chemical reactions. Active free radicals in the flame, like OH (hydroxyl) and CH (methylidyne), are highly reactive molecules that react with the surface of the probe. This reaction releases additional heat, causing the probe to overestimate the actual flame temperature.
Heat flux sensors
A more accurate and faster way of assessing the thermal environment is with heat flux sensors. Unlike temperature measurements, which require thermal equilibrium, heat flux measurements enable quicker intervention since they measure the rate of heat transfer. This allows for preventative measures against unfavourable temperature conditions, such as overheating. Heat flux measurements in industrial furnaces can be categorised into three types (see Figure 1):
- Radiative heat flux: measures heat radiated from flames or hot surfaces.
- Conductive heat flux: measures heat going through the furnace wall.
- Convective heat flux: measures heat transferred by moving gases or liquids, critical for ensuring even temperature distribution.
To differentiate between radiative and convective heat flux, industrial heat flux sensors are often designed with black-coated or metallic surface. The black-coated surface absorbs all radiation and is sensitive to both radiative and convective heat flux, while the metallic surface reflects radiation and is sensitive to convective heat flux only. By subtracting the two measurements, the radiative flux can be isolated.
This principle mirrors the functionality of Hukseflux’s black and gold stickers, used for sensors like the FHF05 and HFP01 in non-industrial applications. Industrial heat flux sensors from Hukseflux can be ordered with or without the black coating.
Most methods for measuring heat flux through furnace walls do not measure the true heat flux, because of the harsh environment. Additionally, the sensor disturbs the heat transfer surface. A thickened wall caused by a heat flux sensor acts as an insulating barrier, leading to an underestimation of the true heat flux. However, recent developments in heat flux sensors have made them more accurate, compact and durable.
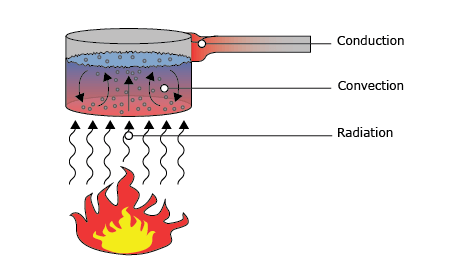
conductive, convective and radiative.
Thermal cameras
Thermal cameras offer a non-invasive method for measuring surface temperatures by capturing infrared radiation. These devices capture the temperature distribution over a large surface area and identify potential hot or cold spots.
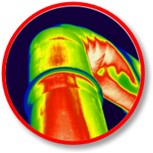
However, installing thermal cameras in industrial furnaces can be a lot more complicated than using heat flux sensors due to the need for proper placement and data processing. Since most thermal cameras can only withstand temperatures up to 50 °C, a minimum distance of 1.5 meters from the flame is usually recommended. Flames and hot gases can obscure the camera’s view or distort the readings. Special filters are often required to improve accuracy by allowing the camera to “see through” these obstructions.
While thermal cameras cover more surface, they are usually more expensive than heat flux sensors. Additionally, since thermal cameras only measure surface temperatures, mathematical modelling of heat flux is required. Therefore, it is advisable to use thermal cameras in combination with heat flux sensors for a more comprehensive analysis.
Why measuring heat flux is important
Heat flux measurements in industrial furnaces, such as those used in the steel and petrochemical industries, are essential for various reasons. For example:
- In crude oil refining, industrial furnaces heat oil to temperatures above 400 °C as it flows through furnace tubes. Keeping the tube surface temperature within a controlled range is vital for preventing equipment failure. If the tubes exceed the optimal temperature by 50 °C, equipment designed to last 25 years may fail in just five years.
- In metal production, maintaining optimal temperatures ensures product quality. For instance, during smelting processes, temperatures that are too low may leave impurities in the metal, while excessively high temperatures can cause issues like excessive carbon absorption, weakening the final product.
Measuring heat flux also ensures safety by detecting hot spots, allowing operators to prevent dangerous situations like overheating or even explosions. On the other hand, operating the furnace below its optimal temperature reduces efficiency, making precise heat flux measurements essential for optimising performance and maintaining safety.
Additionally, optimising performance reduces energy consumption, which not only saves costs but also minimises the environmental impact. This contributes to sustainable industrial practices while maintaining output quality.
Overview of industrial heat flux sensors
The high temperatures and corrosive gases in industrial furnaces create a harsh environment for measurement instruments, impacting the reliability and lifespan of heat flux sensors. This makes it crucial to choose durable, robust sensors to prevent frequent replacements or malfunctions. Hukseflux offers a wide range of high-quality heat flux sensors for industrial use, see Table 1 below.
Table 1 Heat flux sensors for industrial use offered by Hukseflux.
Model | Measurand | Measurement range | Temperature range(1) | Response time | Suggested use |
SBG01 | Heat flux (radiative) | (5, 10, 20, 50, 100, 200) x 103 W/m2 | -30 to +80 °C | < 450 x 10-3 s | Fire testing |
SBG04 | Heat flux (radiative) | 100 x 103 W/m2 | -30 to +80 °C | < 250 x 10-3 s | Calibration reference for cone calorimeters |
GG01 | Heat flux (radiative) | (250, 500, 1000) x 103 W/m2 | -30 to +800 °C | < 250 x 10-3 s | High heat flux measurements |
IHF01 | Heat flux (conductive), temperature | (-1000 to +1000) x 103 W/m2 | -30 to +900 °C | 60 s | Trend-monitoring, comparative measurement, surface temperature |
IHF02 | Heat flux (conductive, temperature | (-100 to +100) x 103 W/m2 | -30 to +900 °C | 210 s | Trend-monitoring, comparative measurement, surface temperature |
HF02 | Heat flux (radiative), temperature | 0 to 15 x 103 W/m2 | -50 to +300 °C(2) | 180 s | Outdoor flare monitoring |
HF05 | Heat flux (conductive), temperature | (-6 to +6) x 103 W/m2 | -30 to +170 °C | 300 s | Industrial heat flux measurements, performance evaluation of industrial insulation |
HFS01 | Heat flux (radiative), temperature | 0 to 800 x 103 W/m2 | -30 to +650 °C | 60 s | Solar concentrators, flame research, fluidised beds |
1. Continuous use, see website for short interval temperature ratings (if applicable).
2. Operating temperature, measuring range is -30 to +100 °C.
There are many more specifications to consider besides the ones mentioned in the table above. Visit our website for a detailed description of each heat flux sensor, and feel free to contact us for personalized recommendations.
Conclusion
Accurately measuring heat flux in industrial furnaces is essential for optimising performance, ensuring safety, extending equipment lifespan, improving product quality, and reducing both costs and emissions.
While temperature measurements are useful, they only provide part of the picture. Heat flux measurements, combined with advanced tools like thermal cameras, provide a faster and more comprehensive view of the thermal dynamics inside furnaces.
Despite the challenges associated with sensor durability and accuracy, choosing the right heat flux sensor can significantly improve furnace efficiency and operational safety. Hukseflux’s wide range of heat flux sensors offers reliable solutions for various industrial applications, ensuring that you can meet your specific needs and challenges.